In industrial applications, the choice of pump technology can significantly affect efficiency, reliability and overall operating costs. Among the many types of pumps, centrifugal pumps and positive displacement pumps are the two most widely used. Each pump has its own unique advantages and applications, and understanding how they work together can help optimize performance in various fields such as petroleum, shipping, and chemicals.
Centrifugal pumps work by converting rotational energy (usually from a motor) into fluid kinetic energy. This is achieved through the use of an impeller, which accelerates the fluid from the center of the pump outward. The result is a continuous flow of liquid, which makes centrifugal pumps ideal for applications requiring high flow rates and low viscosity fluids.
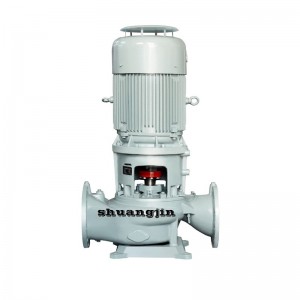
Positive displacement pumps, on the other hand, work by trapping a volume of fluid and forcing it into a discharge pipe. This mechanism enables them to handle high viscosity fluids and provide a constant flow rate regardless of pressure changes. Positive displacement pumps are particularly useful in applications that require precise metering or high pressures.
EMC pumps: the versatile solution
The EMC pump is one of the best on the market, combining the advantages of centrifugal and positive displacement technologies. This robust casing pump is firmly connected to the motor shaft, ensuring stability and reliability during operation. Its design gives it a low center of gravity and height, making it ideal for pipeline pumping applications. The suction and discharge ports are in line, which helps to achieve efficient fluid transfer.
In addition, the EMC pump can be converted into an automatic self-priming pump by adding an air ejector. This feature enhances its versatility, enabling it to be used in a variety of industrial environments, from power stations to food processing plants.
The role of centrifugal pumps and positive displacement pumps in industry
In many industrial applications, the combination of centrifugal and positive displacement pumps can improve performance. For example, in the oil industry, centrifugal pumps are often used to transfer crude oil due to their large handling capacity. However, when viscous fluids need to be transferred or precise metering is required, positive displacement pumps become essential.
In chemical processing, where precise flow rates and the ability to handle corrosive materials are critical, the integration of both types of pumps is vital. Centrifugal pumps can efficiently move large volumes of chemicals, while positive displacement pumps ensure the right amount of chemical is delivered to where it is needed.
in conclusion
The synergy between centrifugal and positive displacement pumps represents the progress of pump technology. Companies specializing in the production of such pumps, such as those that offer EMC models, are always at the forefront of innovation, serving a wide range of industries such as machinery, metallurgy, construction and environmental protection.
By understanding the benefits of each pump type and how they work together, industries can optimize operations, reduce costs and improve overall efficiency. As technology continues to advance, the synergy between centrifugal and positive displacement pumps will undoubtedly play a key role in shaping the future of industrial applications.
Post time: Jul-21-2025