In the field of fluid dynamics, pumps play a vital role in various industries from petroleum to chemicals. The most commonly used types of pumps include centrifugal pumps and screw pumps. Although the main function of both is to move fluids, they work differently and are suitable for different applications. In this blog, we will explore the main differences between centrifugal pumps and progressive cavity pumps to help you make an informed decision based on your business needs.
Centrifugal Pumps: The Workhorse of Fluid Transport
Centrifugal pumps are widely recognized for their efficient fluid transfer capabilities. They work by converting rotational energy (usually from an electric motor) into kinetic energy of the fluid. This is achieved by imparting velocity to the fluid through a rotating impeller, which is converted into pressure as the fluid exits the pump.
One of the outstanding features of centrifugal pumps is their ability to handle large volumes of relatively low viscosity fluids. They are particularly effective in applications involving water, chemicals and other low-viscosity liquids. For example, the C28 WPE Standard Chemical Process Pump is a horizontal, single-stage, single-suction centrifugal pump designed specifically for the petroleum industry. It complies with stringent standards such as DIN2456 S02858 and GB562-85, ensuring reliability and performance in harsh environments.
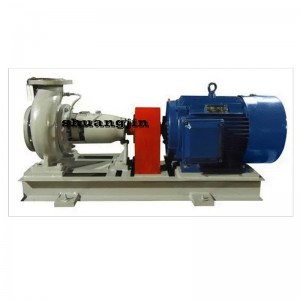

Screw pumps: precise and versatile
Progressive cavity pumps, on the other hand, work on a different principle. They utilize one or more screws to move fluid along the axis of the pump. This design allows for a continuous flow of fluid, making progressive cavity pumps ideal for handling high-viscosity liquids and slurries. The unique mechanism of a progressive cavity pump enables it to maintain a steady flow rate, unaffected by pressure changes, making it ideal for applications where precision is critical.
Screw pumps are particularly advantageous in industries that require the transportation of high-temperature media or special fluids. Their independent annular heating chamber design can provide sufficient heating without causing deformation of related components, ensuring that the pump can effectively meet the requirements for transporting high-temperature media.
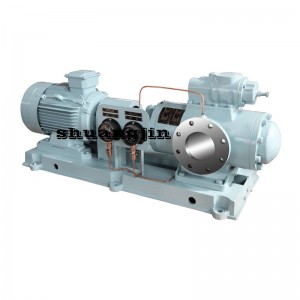
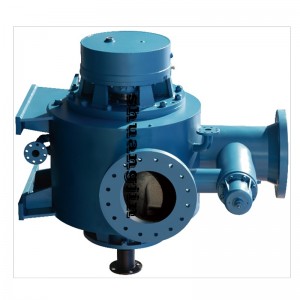
Main Differences: Quick Comparison
1. Working Principle: Centrifugal pumps use rotational energy to generate pressure, while screw pumps rely on the movement of the screw to transport fluid.
2. Fluid handling: Centrifugal pumps are good at handling low-viscosity fluids, while screw pumps are more suitable for high-viscosity liquids and slurries.
3. Flow characteristics: The flow rate of a centrifugal pump will fluctuate as the pressure changes, while a screw pump provides a consistent flow rate.
4. Temperature handling: Screw pumps are designed to handle high temperatures and special media, making them more versatile in certain applications.
5. Maintenance and Lifespan: Centrifugal pumps typically require more maintenance due to impeller wear, while screw pumps tend to have a longer lifespan due to their rugged design.
Conclusion: Choose the pump that suits your needs
When choosing between centrifugal and progressive cavity pumps, it is important to consider the specific requirements of your application. Factors such as fluid viscosity, temperature, and flow rate will play a big role in your decision making process.
At our company, we always put customer satisfaction, honesty and credibility first. We are committed to providing high-quality products and services to contribute to the national economy and the international market. We welcome colleagues from all walks of life at home and abroad to discuss cooperation. Understanding the difference between centrifugal pumps and screw pumps can help you make an informed choice to improve operational efficiency and succeed in your industry.
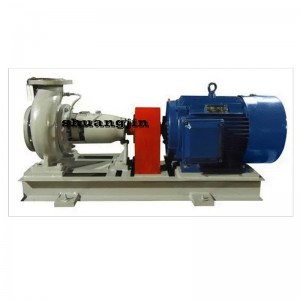
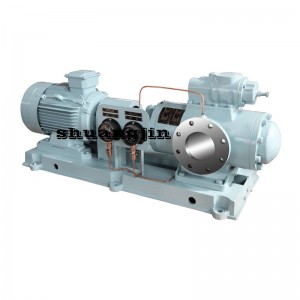
Post time: Jul-25-2025